TeReGeo - Simulation of micro-detonations used for deep-drilling in geothermal applications
Background
Due to the ever growing energy demands it is necessary to explore new CO2-neutral forms of energy. Methods that do not depend on special localised conditions (e.g. Wind-, Tidal- and Hydropower) should be favoured as they provide reliable and independent operation of local energy providers. Nowadays geothermal energy is only used in very few parts of the world because of the lack of suitable exploration methods (deep drilling).
Other advantages of geothermal energy are the ability to cover base loads and the lack of additional costs for fuel.
Generally speaking geothermal energy is available in sufficient amounts from 10km depth but until now has not been feasibly explorated. The costs for drilling in oil and gas exploration rise exponentially with increasing depth and from approximately 5km are not feasible anymore. The holes used in mechanical drilling methods are conical with a diminishing cross sectional area with increasing depth which has negative effects on the usage of available geothermal energy. These are reasons for developing a new drilling method which is economic for great depths.
Methods for usage of geothermal power
Different methods are used for extraction of geothermal power. Generally water or a mixture of water and other components is evaporated and the steam is converted to electrical energy in a power plant. Until now these types of power plants could only be operated in geothermally active regions (e.g. close to vulcanos in iceland, canada, etc.). If it becomes possible to explore available heat in great depths power plants of this type can be installed anywhere.
On one hand the most common method for using geothermal power ist the "hot-dry-rock" method where heat stored in dry rocky material is used. On the other hand subterranean hot water reservoirs are used to directly extract the heat using heat exchangers that power steam cycles. The first method is used much more frequently and could result in widespread usage.
Using the "hot-dry-rock" method the heat-reservoir (i.e. porous rocky material) is explorated with two to three drillings. One of the holes is used for water supply. The generated steam is taken out through the other two holes and used as a heating medium in a steam cycle. As the usual temperatures of the steam taken out of the rock are not ideal for established Clausius-Rankine-Processes other processes like the ORC and the calina-process were developed.
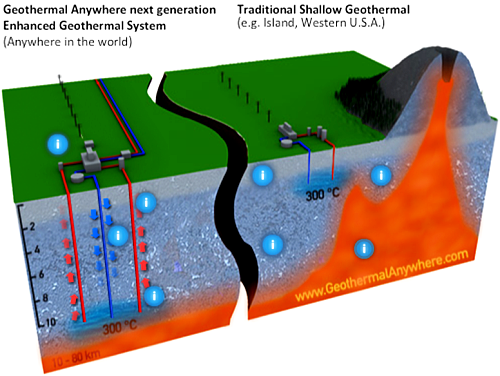
Fig. 1: Comparison of traditional and future use of geothermal energy
Realisation of economic deep drilling
Completely new concepts have been developed for economic deep drilling. Existing technologies could not be adapted in a useful way. One of the biggest problems is the uninterupted contact to the surface using the drill rod and also the wear of the drilling head. A possible solution to this problem is contact-less drilling.
Amongst many other methods of contact-less drilling of hard material micro-detonations were evaluated. To find the ideal impact of micro-detonations on the rock possible designs of machines for creating these micro-detonations should be simulated and optimised.
Simulations of micro-detonations
A general concept of realisation for contact-less deep-drilling was proposed by a slovak research company and should be optimised by application of Computational Fluid Dynamics (CFD) in collaboration of the research groups of Franz Winter and Michael Harasek at the Institute of Chemical Engineering at the Vienna University of Technology.
The contact-less abrasion is realised through guided acceleration of reaction gases of a detonation in a conical tube and the subsequent impact of water driven by high pressure onto rocky material - which is comparable to waterjet cutting. A full simulation of all physical effects would consider supersonic flow, multiphase flow, shock waves and would be too complicated to start. A simplified analysis of the process was conducted to evaluate the realisability of the complete process.
The search for a suitable fuel
A suitable fuel for generation of micro detonations should have following properties: high specific energy density, high flamability, low iginition delay, low environmental toxicity and uncomplicated handling. Simulations of a flow tube were used to study the behaviour and applicability of different fuels for deep drilling applications.
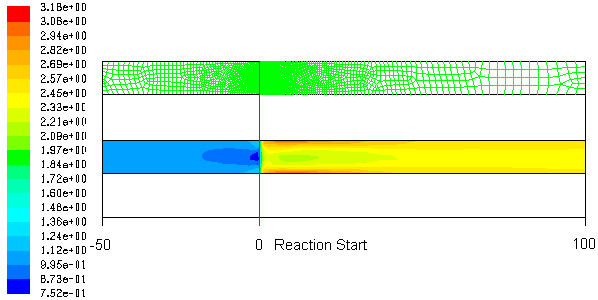
Fig. 2: Contours of gas velocity in a flow tube
Furthermore it is necessary to develop a suitable chemistry model for combustion simulations. The difficulty in combustion chemistry is the number of reactions that vastly increases simulation time. Therefore a simplified model was developed for combustion, which is accurate enough and only slightly increases simulation time.
Preparation of a suitable simulation environment
Like mentioned above the simulation of the problem poses a great challange. As most well established software packages for fluid-dynamic simulations had difficulties in simulating supersonic multiphase flows the open source software OpenFOAM(R) was used. A new solver was implemented by József Nagy. To cope with complex multiphase flow an existing solver was used as a template and extensions for temperature dependent equations of state for compressible gaseous and liquid phases were written. (Under these extreme conditions liquids can not be treated as incompressible anymore.)
The said solver was validated with several previously published test cases.
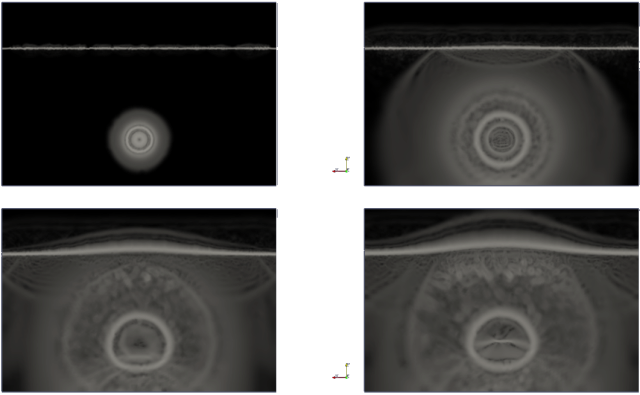
Fig. 3: Simulation of an unterwater explosion using the newly developed solver
Outlook and acknowledgements
The solver for the multiphase flows is already tested and ready to use. The simplified combustion model will be finished soon. When it is available different conditions of the micro-detonation machine can be simulated und optimised.
This work was funded by the European Regional Development Fund for cross border collaboration (Slovakia/Austria 2007-2013). Acknowledgements go to our project partners of Celim, Slovakia.