Effect of Different Diesel Fuel Nozzle Holes Geometries on Cavitation
Cavitation is the primary cause of the effective flow area reduction in fuel nozzles and mechanical damage, leading to increased pressure losses. However, cavitation is known to improve the spray breakup processes. The damaging effects on the fuel injection performance can be caused by cavitation, e.g., flow instabilities, excessive noise generation, and erosion, which can cause deterioration to the injector and nozzles. The occurrence of cavitation in the spray hole is a typical phenomenon, particularly for diesel injectors. It means that at least at the point where cavitation occurs, the vapor pressure of the liquid is locally undershot, and cavitation bubbles are formed as a result. These bubbles are transported with the fluid, and depending on the environmental conditions, they can grow, shrink or implode. The main focus of this research is to extend the knowledge about the correlation between nozzle geometry and cavitation.
It is challenging to produce a nozzle prototype with different internal geometries in a 0.4mm hole. The current technologies and measurement equipment are limited to prove the manufacturing according to the design. Therefore, we are strongly reluctant on CFD simulations. We use this virtual prototyping to pre-evaluate the nozzle geometry to control the cavitation and enhance the air-fuel mixture. The significant advantage of virtual prototyping is the fast and resource-conserving development. We examined the effect of different nozzle hole geometries on the level of cavitation and vapor fuel concentration by simulating the fuel injection process with the OpenFOAM® solver cavitationFoam. These simulations are focused on the cavitation's effect expressed in terms of the vapor concentration of fuel after a determined time. Chemical reactions for the combustion process or atomization of the fuel droplets are out of the scope of this study.
The velocities and vapor distributions are non-homogeneous in the downstream chamber, but the cavitation level can be controlled and modified. The rounding at the nozzle inlet is the leading reason for the flow's increased velocity and the cavitation level reduction. However, as the cavitation reduces, the vapor fuel concentration does, too; cavitation is a phenomenon that enhances fuel atomization. Figure 1 and Figure 2 show the base case (cylindrical nozzle) and nozzle with an expanded section.
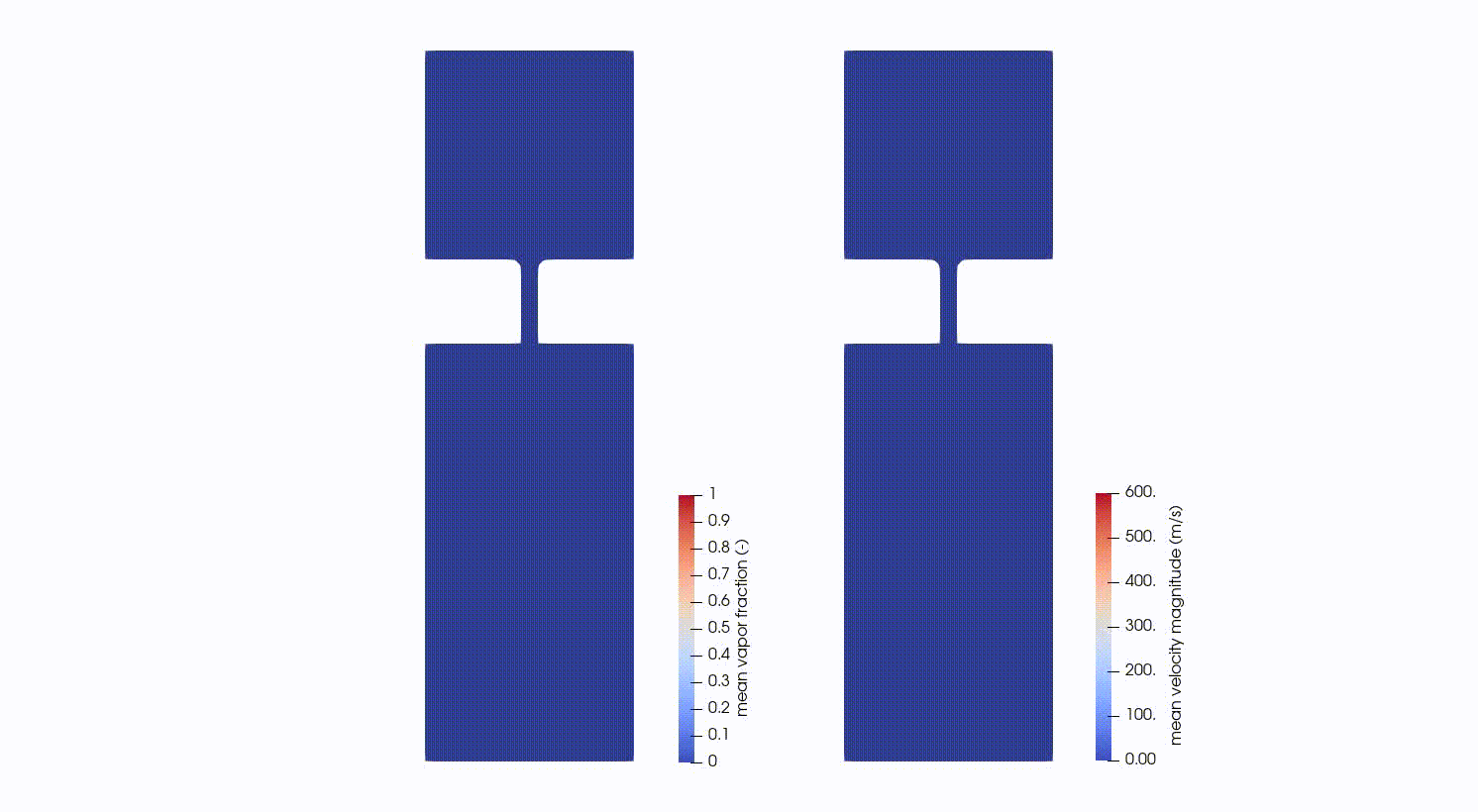
Fig. 1: Mean gas phase fraction (left) and mean velocity magnitude (right) of the base nozzle case.
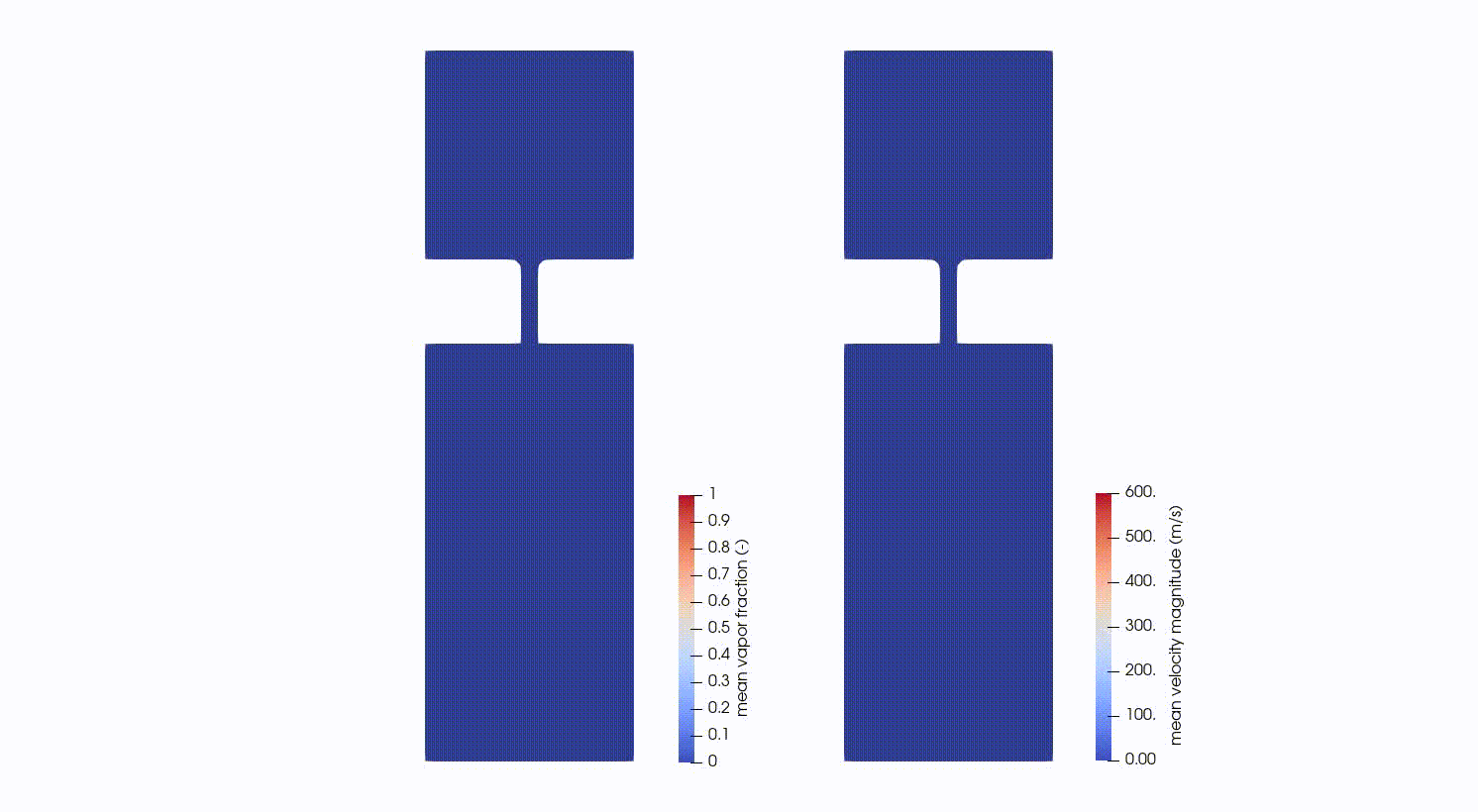
Fig. 2: Mean gas phase fraction (left) and mean velocity magnitude (right) of the nozzle with expansion case.
More details about this research can be found in the associated SAE Technical Paper.